Established in 1995, Posiva Oy is an expert organization in environmental technology that is tasked with handling the final disposal of spent nuclear fuel for its owners. Posiva is owned by Teollisuuden Voima and Fortum Power and Heat. The organization is in charge of the research, development and planning operations for the final disposal facility Onkalo, which is located at Olkiluoto in Eurajoki. Furthermore, Posiva handles the implementation and operation of the plants.
Finland is the first country in the world to start the final disposal of spent nuclear fuel. This is partly due to reasons unrelated to Posiva.
– For example, Sweden was supposed to start final disposal operations before us, but there have been licensing delays in other countries. In Finland, we have been able to progress quite consistently and keep to the schedule, says Petteri Vuorio, Engineering Manager for Posiva, who is responsible for plant engineering.
The solution must be secure even after a thousand years
Posiva’s facilities at Olkiluoto comprise an overground encapsulation plant, where the fuel is encapsulated inside canisters, and an underground final disposal plant in which the final disposal canisters are placed.
The deposition tunnels are excavated in bedrock some 400–450 m underground. This way, the fuel can be isolated from the living environment, avoiding any overground or atmospheric changes from impacting the final disposal repository. The excavation follows years of research and development efforts.
– The handling of radioactive materials poses particular challenges in the design of the plant and its systems and sets requirements on system reliability, among other things. Another thing to note is long-term safety, which is necessary for the final disposal solution – we are talking about a time span that extends more than 100,000 years into the future, and we must be able to ensure the safety of the solution the entire time, Mr. Vuorio explains.
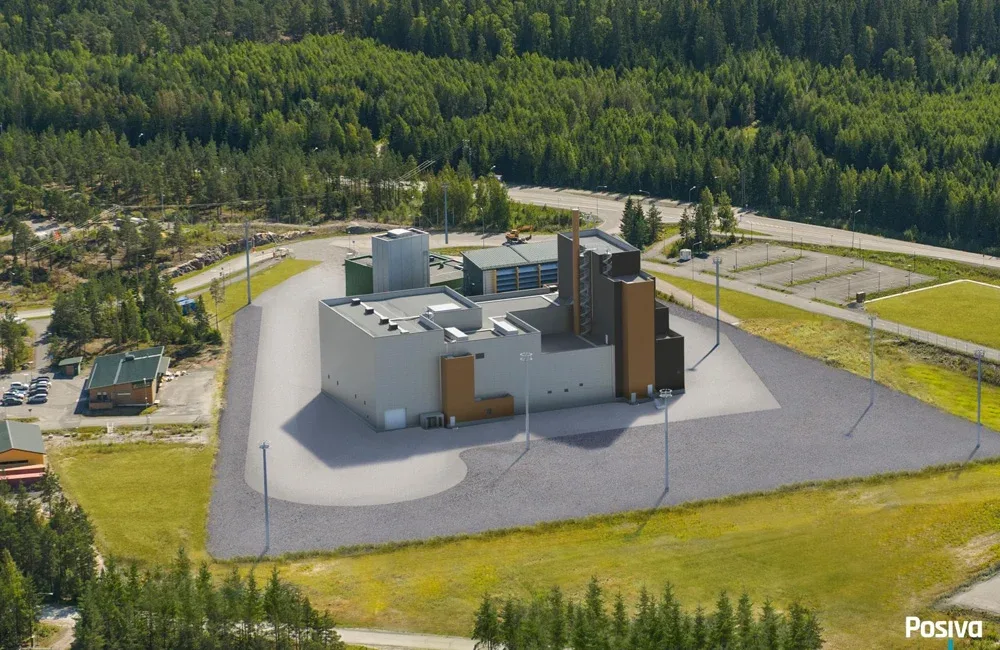
The project schedule that was prepared in 1983 specified that the final disposal site would be chosen at the turn of the millennium, the construction would start in the 2010s, and the operation of the facilities would start a decade later. This schedule has worked out: Olkiluoto was chosen as the final disposal site in 2001, the excavation of the first tunnels started in 2004, and the implementation of the first five actual deposition tunnels began in May 2021. Today, the total length of the tunnel system is already approximately 10 kilometers.
The aim is to start the actual final disposal activities in the mid-2020s. This means that unmanned vehicles will drive inside the tunnels and transport uranium assemblies encapsulated inside final disposal canisters. The canisters are placed inside deposition holes drilled in the tunnel floor and lined with blocks of bentonite clay. Once a deposition tunnel has been completely filled, a thick concrete plug is cast at the mouth of the tunnel.
Mr. Vuorio says that reliability and compliance are essential in the encapsulation of nuclear fuel and the final disposal of the canisters so that the canisters do not experience any disturbances that jeopardize safety even in the long term.
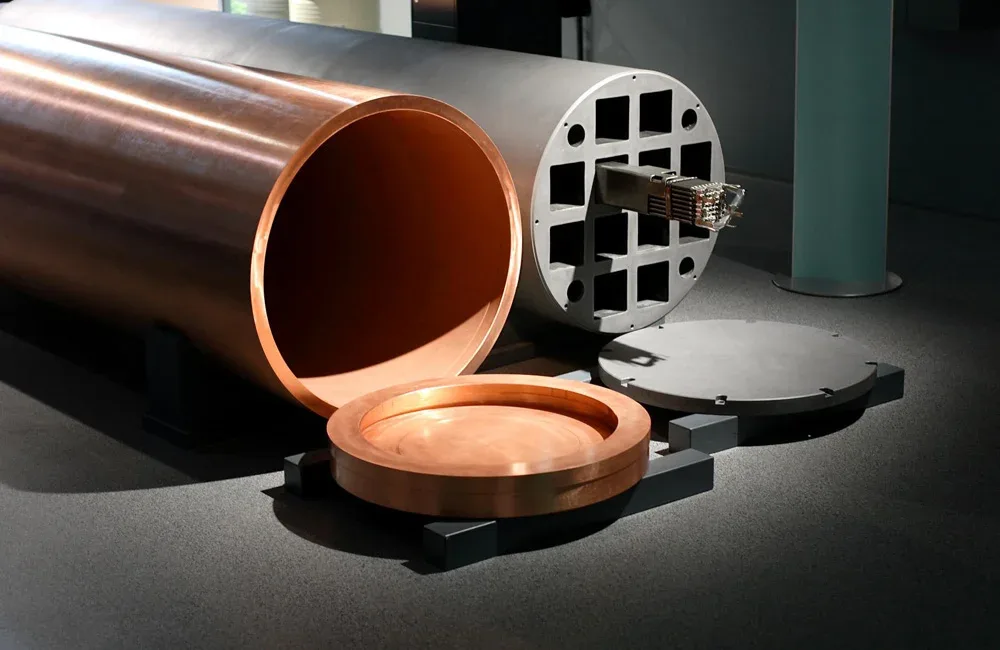
A good automation partner understands the characteristics of the plant
– Posiva cannot implement everything on its own and, therefore, partners are heavily involved in the project. The selection of suppliers for design tasks and systems delivery is one way of ensuring that the various stages including design, manufacturing, installation, and commissioning are completed against high standards of quality while meeting the set requirements, Mr. Vuorio emphasizes.
Insta has participated in the implementation of the final disposal solution in various ways. In 2019, the company completed the delivery of the main automation system for the final disposal plant, and the commissioning of the automation delivery for the overground encapsulation plant is now beginning.
Posiva’s collaboration with Insta started with the design and manufacture of the field monitoring equipment used for groundwater research in 2010, and it has included various turnkey deliveries and engineering projects as well as cabinet manufacturing and installation tasks. In total, Insta has delivered or is in the process of delivering approximately 30 projects related to the encapsulation plant and final disposal plant.
At the encapsulation plant, the recently completed docking station for the nuclear fuel transport container was built fully using Finnish knowledge. The docking station acts as the gate between the fuel handling cell and the transfer corridor for the transport container. Insta delivered the equipment automation and electrification for the docking station.
– For us, this is a positive thing. We get synergy benefits in systems design when the implementing party knows the interfaces to which an individual system is connected, Mr. Vuorio explains.
The selection of an automation partner emphasized competence as well as references for similar projects.
– We knew already then that we were choosing a long-term partner. For us, it would have been counterproductive to switch suppliers at each stage of the project. Instead, we wanted to find a good partner who we could work with until the end of the project, Mr. Vuorio says.
He adds that the special requirements for the automation include separating the control systems from the monitoring systems. This way, they cannot influence one another and a potential failure in one system does not cause another subsystem to fail. Good and comprehensive documentation is also important.
– Automation systems can sort of be seen as the brain of the process that, on the one hand, controls the performance of the desired functions and, on the other hand, monitors that the functions are completed within the specified parameters. This also ensures safety, Mr. Vuorio says and continues:
– A good automation partner familiarizes themselves with the particularities of the plant and understands its operation well enough to suggest appropriate implementation solutions that meet our needs. Other important aspects include operating in a reliable, predictable way and delivering on promises so that we can trust things to work out. Because this is a pioneering project, not everything can be fully planned out. Furthermore, the partner needs to have the sufficient scale to meet any surprising resource needs that may arise in the future.
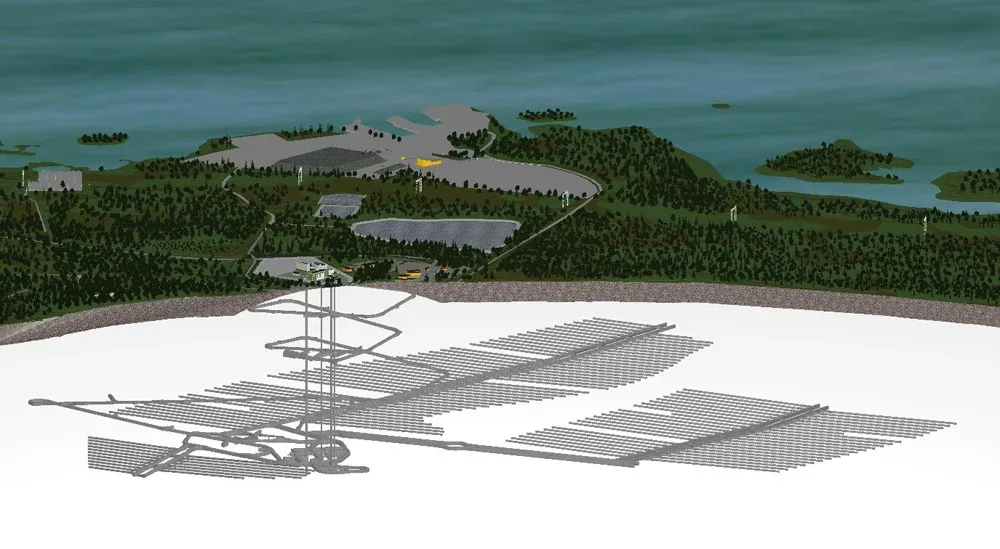
The main automation system handles the infrastructure, processes, and safety
In the underground final disposal plant, the main automation system handles the infrastructure of the plant’s tunnels, taking care of things such as good ventilation as well as inlet and outlet water. The earlier controls from the worksite stage were upgraded to a process control system for better flexibility, expandability, and easier maintenance considering the future.
– As the tunnel system is not completely excavated right at the start but instead expanded gradually, along with other work taking place, the systems must also include provisions for future expansions, Mr. Vuorio explains.
The other task of the main automation system is controlling the actual final disposal process.
– Various pieces of production equipment implement tasks related to the deposition and protection of the canisters. Their controls also incorporate automation and use their own control systems, and all of them are integrated in the plant-level automation system, Mr. Vuorio says.
To give some idea about the scale of the deliveries, just the part that handles the infrastructure is equivalent in scope to the entire automation system of one industrial facility.
Similarly, the automation system of the encapsulation plant can be roughly divided in two sections. The control automation system controls the functions of the different systems and manages the encapsulation process. In addition, a separate protection automation system prevents any potential defects caused by human errors or other reasons from developing into accident scenarios.
– For the protection automation, there were reference implementations available at other nuclear facilities and systems. It is also subject to regulatory requirements and, in our case, they come from the Radiation and Nuclear Safety Authority, Mr. Vuorio adds.
Commendable flexibility and realistic workload assessments
When asked about the smoothness of collaboration, Mr. Vuorio mentions flexibility and realistic assessments of the scope of work.
– All in all, we have been very happy about partnering with Insta and all of the targets have been met so far. As a positive, I can point out flexibility – if there have been changes in terms of the schedules or other aspects, Insta has accommodated them rather well, Mr. Vuorio says.
– Another thing that is not always a given is that we have been able to trust Insta’s workload assessments. This is important from a project management perspective.
Iiro Engren, who is responsible for the encapsulation plant program and its implementation, agrees with the comment on flexibility, and he is also happy with the accurate scope of work estimates.
– In addition, their team has good chemistry with our personnel. I have received good feedback about this and I have also noticed that the people work really well together, he adds.
According to Mr. Vuorio and Mr. Engren, Insta’s strengths include competent personnel and the ability to find solutions to challenges. They consider that Insta’s low employee churn has been a factor in the successful collaboration.
Source for the photos: Posiva Oy
For more information:
Rami Siren
Profit Center Manager, Lifecycle Services
Energy
Insta Automation
etunimi.sukunimi (at) insta.fi
Kimmo Suonperä
Sales Manager, Industry
Insta Automation
etunimi.sukunimi (at) insta.fi