Easy and reliable equipment maintenance
Avoiding disturbances in the electrical distribution system requires systematic and regular equipment maintenance. Preventive maintenance, periodic service and optimized replacement of equipment ensure trouble-free operation and minimize unplanned defects.
The electrical grid can contain thousands of pieces of equipment. Being able to easily find the up-to-date service and inspection data really streamlines the maintenance process. This ensures that periodic maintenance is carried out at the right time and that backup equipment can be found in case of a malfunction.
The iNetti equipment maintenance system is part of Insta’s maintenance service for electrical distribution equipment. It makes the service and maintenance of equipment easy.
iNetti helps to overcome the challenges in the maintenance of electrical distribution equipment
iNetti displays the service status of all equipment. It helps ensure the timely performance of periodic maintenance – the system reports planned maintenance needs in advance and displays the schedule for the next maintenance task for each piece of equipment as well as the type of the task, such as thermal imaging, relay testing, circuit breaker service, transformer service, oil analysis, etc.
In iNetti, you can find the up-to-date service documentation for each piece of equipment, such as service records, drawings and software. It allows the real-time monitoring of contracted service and checking whether a service is overdue, completed or if additional measures are needed.
The customer can easily communicate with maintenance via the system.
The software is easy to use in the desktop view as well as on mobile devices. The equipment-specific log allows for recording malfunctions or disturbances concerning an individual device.The comprehensive search functionalities enable searching iNetti by equipment type, location or action, for example.
iNetti typically includes the following equipment: switchboards, transformers, switchgear, low and high voltage breakers, disconnectors), protective relays, compensators, UPS equipment and battery systems, AC/DC drives and motors.
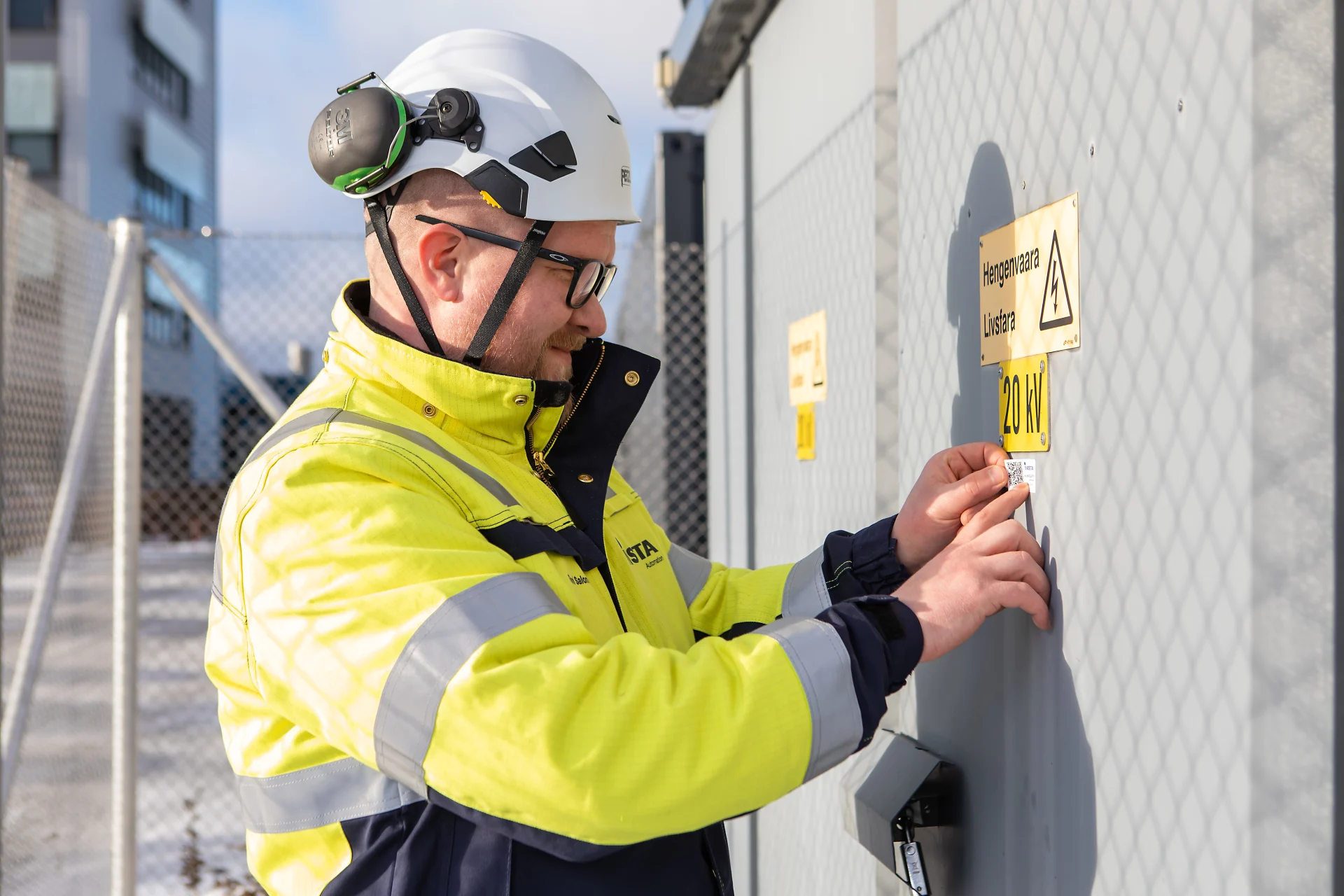
Real-time tracking of the contracted service
The tracking of equipment service is made easier through QR codes that are linked in iNetti. The QR code replaces the conventional service label. Having a label with a QR code on a device makes it quicker to find the right piece of equipment in the system. The QR code leads to a page that contains the five previous and five future service tasks. A person with iNetti credentials can use the link to examine the detailed service history of the device. The service data is located on a dedicated, protected domain, which ensures the solution’s data security.
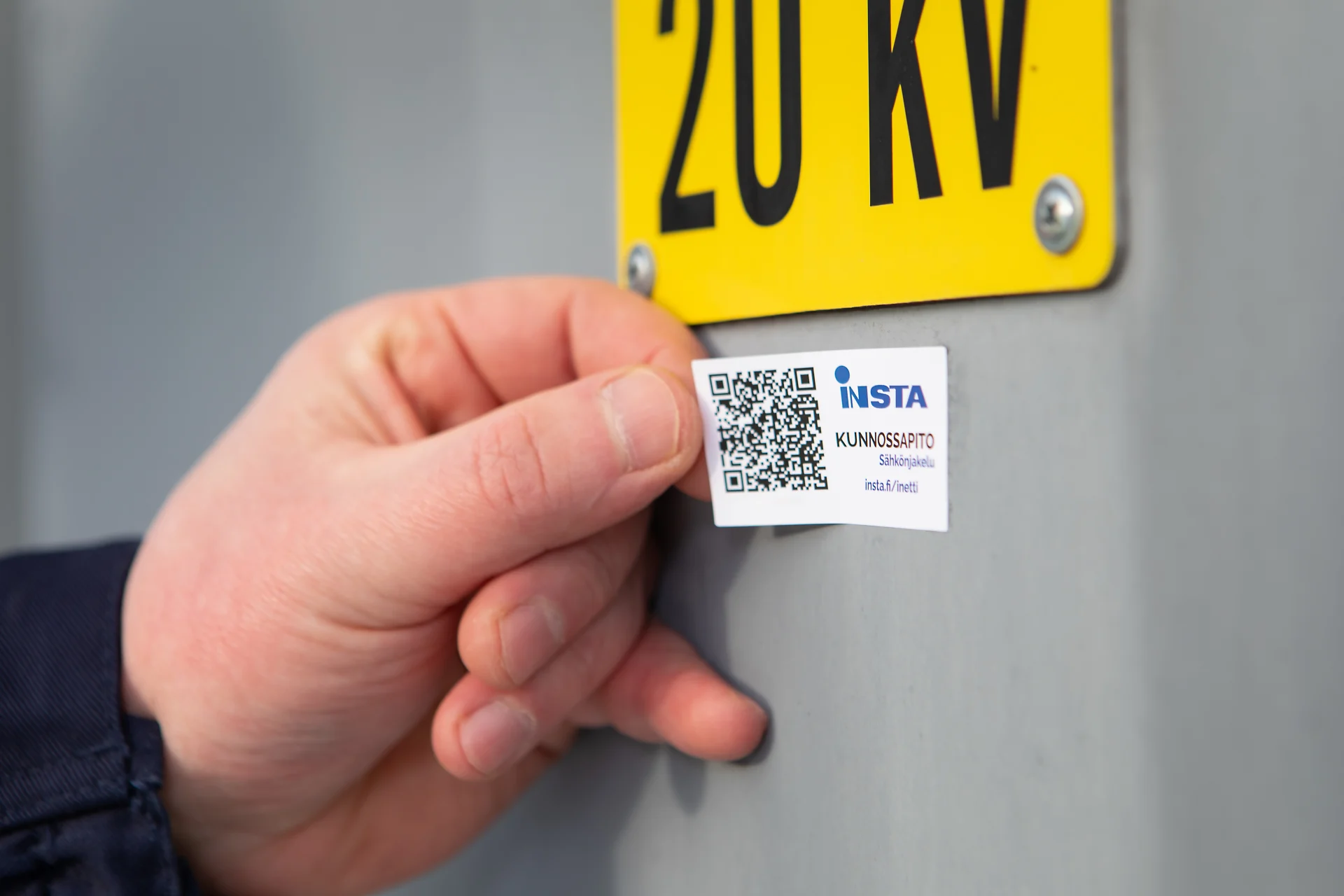
Easy to set up
The first step in setting up iNetti is mapping out the electrical distribution equipment, which includes specifying the type and number of each device. After this, the equipment is defined in iNetti, e.g. by utilizing the electrical distribution systems’ main diagrams. Once the equipment has been defined, a preventive maintenance plan that matches the customer’s needs is prepared with the customer. The price for the maintenance service is determined by, among other things, the amount of equipment and number of software users.
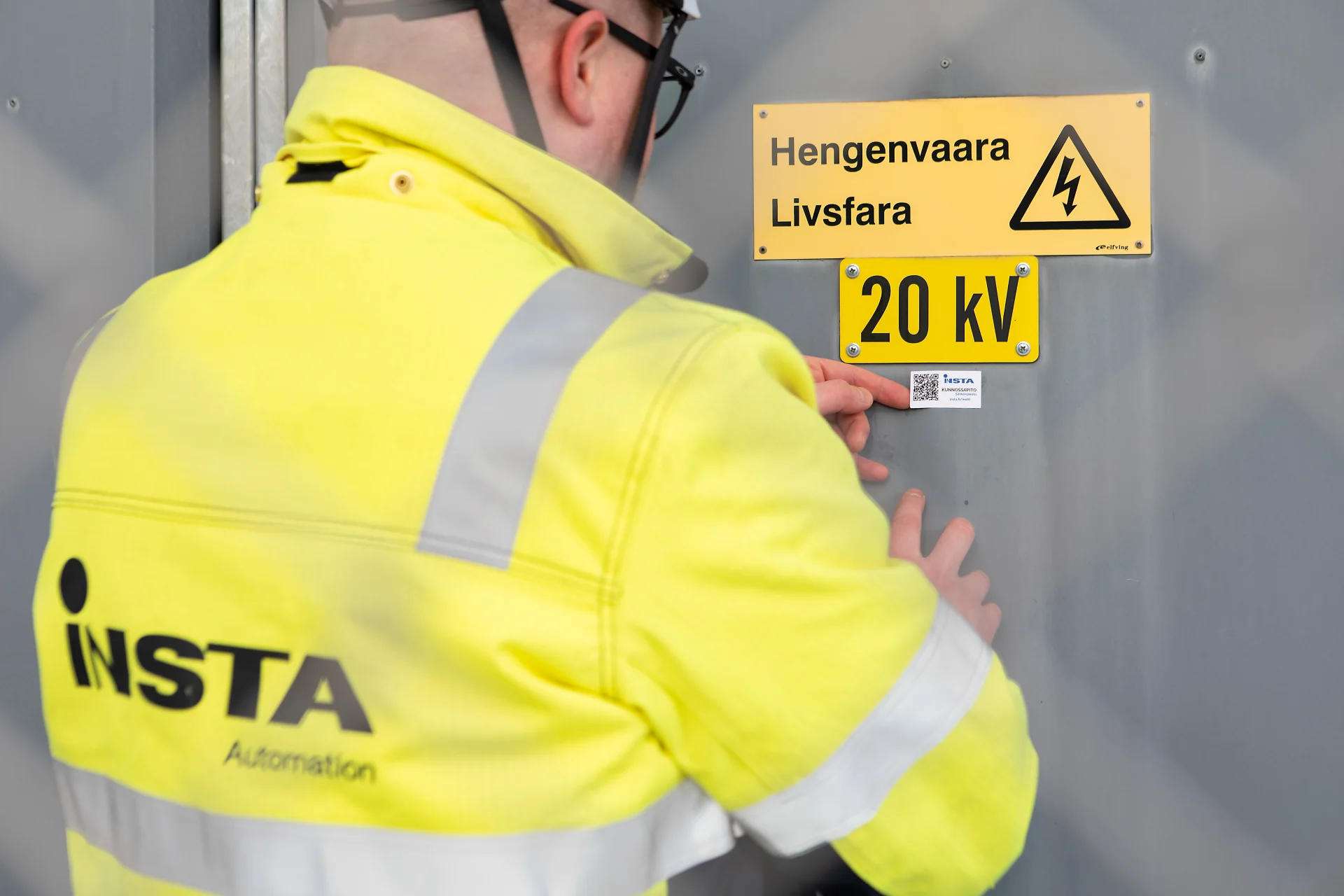
The iNetti system collects in one place the equipment that requires periodic maintenance
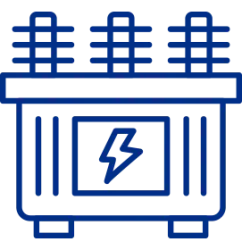
Transformers
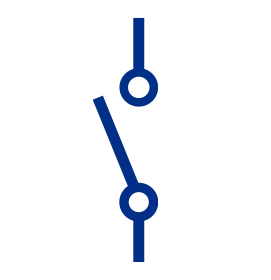
Disconnectors
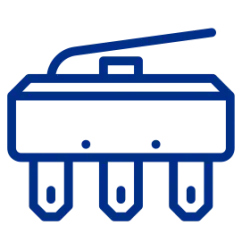
Relays
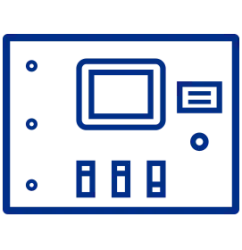
Compensators
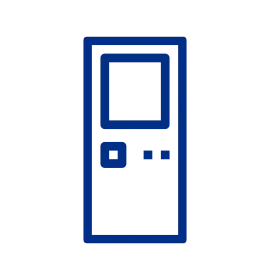
Frequency converters
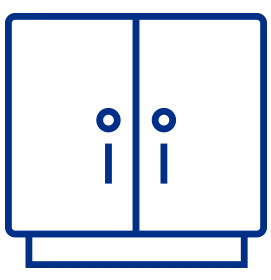
Low- and medium-voltage switchboards
Life-cycle services for electrical distribution equipment
As a life cycle partner in electrical distribution, we will ensure the timeliness of customer investments and apply equipment maintenance practices to prevent uncontrolled breakdowns and production outages.
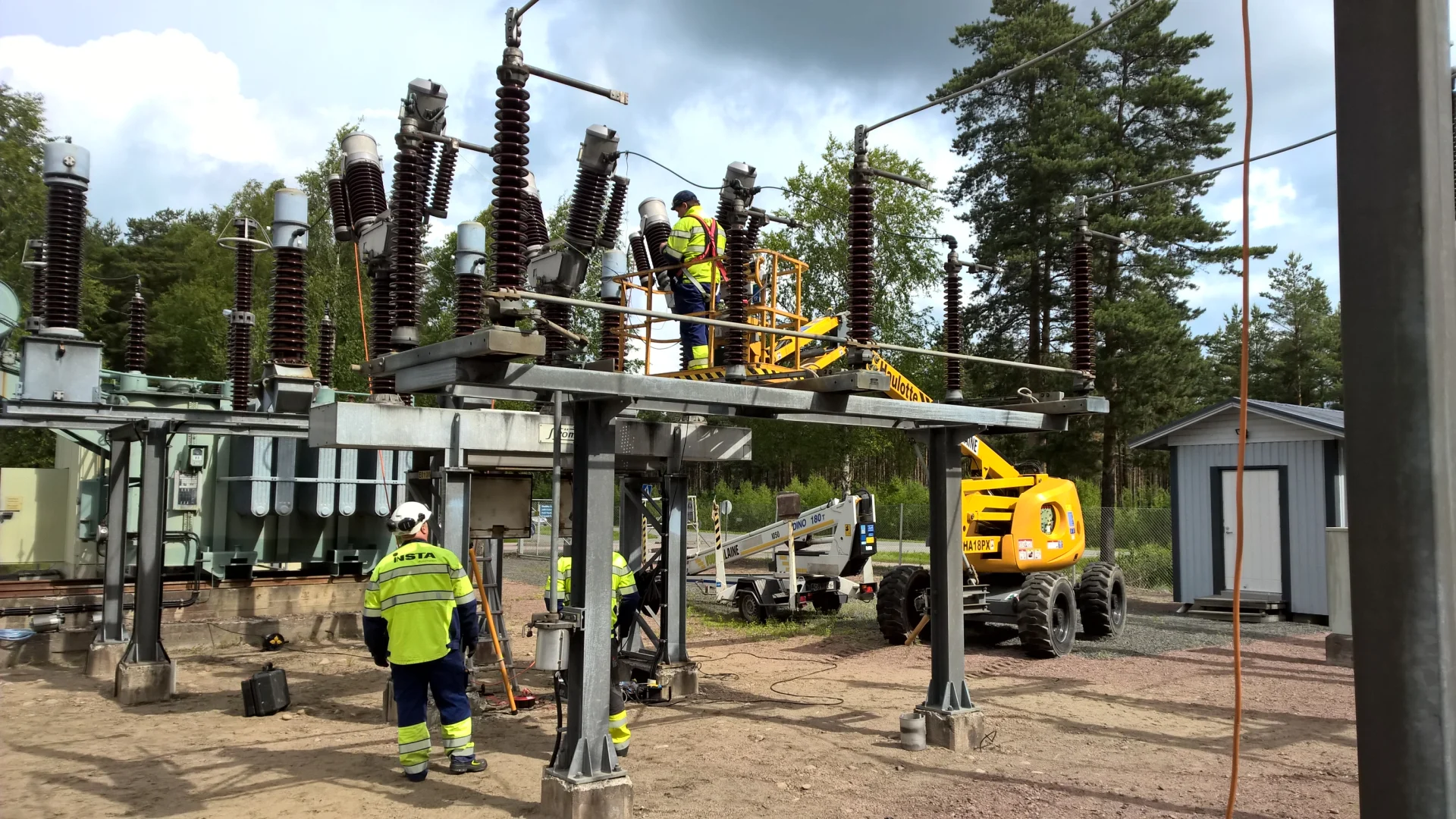