Koneoppiminen on teollisuudessa hyvä työkalu, joka tarjoaa mahdollisuuden kasvattaa liiketoimintaa. Sen avulla voidaan pitää prosessiautomaatio kustannustehokkaasti optimoituna ja hyödyntää jatkuvan parantamisen menetelmiä.
Insta ja metallialan yritys Boliden Harjavalta tutkivat Bolidenin rikkihappotehtaassa, pystytäänkö rikkihappotehtaan kaasunjakoprosessia optimoimaan tekoälyn avulla. Yhteisprojektissa yhtiöt onnistuivat mallintamaan prosessin osan neuroverkon avulla.
– Installa on kyvykkyys hyödyntää koneoppivia algoritmeja säätöjen analysoinnissa ja niiden kyvykkyyden parantamisessa. Meillä on myös asiakas, joka ymmärtää tämän arvon. Pilotoinnin mahdollisuus oli meille todella tärkeä, toteaa Insta Automationin Aluetoiminta ja kunnossapito -liiketoimintayksikön johtaja Mika Riikonen.
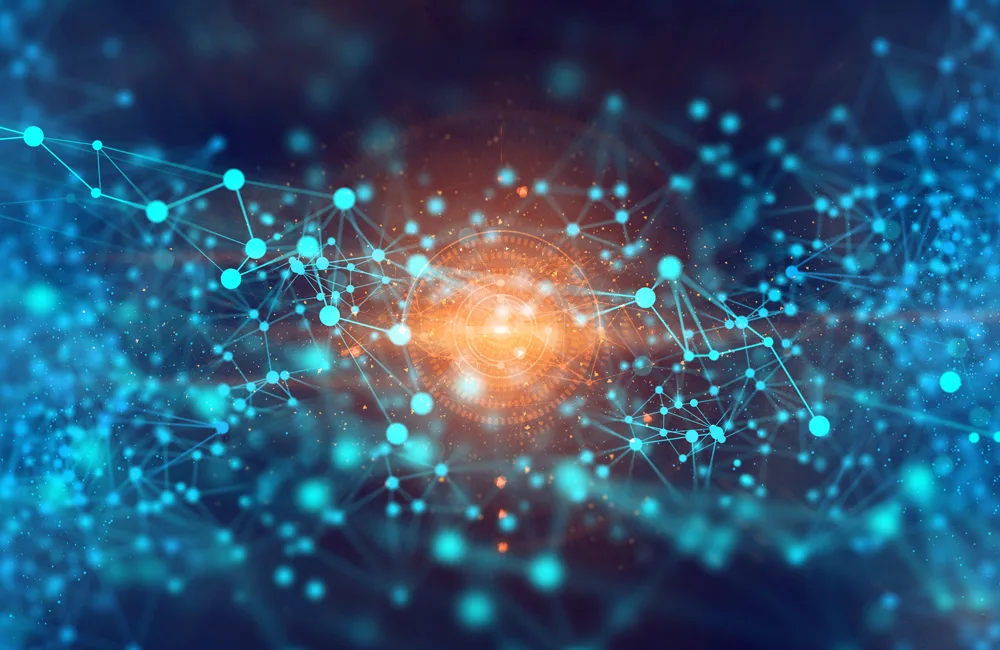
Säätäjien optimoinnilla tunnistetaan hyödyt
Boliden Harjavallassa säätäjä ja sen ohjaus mallinnettiin uudestaan ja kokeiltiin mallin avulla, miltä tulos näyttäisi. Tuloksena syntyi eräänlainen digital twin, digitaalinen kaksonen, jonka avulla Boliden Harjavalta pystyy simuloimaan tuotantoa erilaisilla ajoparametreillä ja vähentämään päästöjä.
Tulokset osoittivat, että rikkidioksidipäästöjä on mahdollista pienentää 5–10 prosenttia. Koska hyöty on merkittävä, simuloitu malli koodataan automaatiojärjestelmään.
– Säätäjien optimoinnista on paljon muutakin hyötyä: esimerkiksi ympäristöturvallisuus ja työturvallisuus paranevat, energiankulutus vähenee, raaka-aineen hävikki pienenee sekä tuottavuus kasvaa, Riikonen toteaa.
Koneoppimisella älykkääseen kunnossapitoon
Jatkossa dataa hyödynnetään teollisuudessa yhä enemmän ja koneoppivat mallit tarjoavat kiistattomia hyötyjä myös kunnossapitoon. Tärkeiden vaiheiden yli ei kuitenkaan voi hypätä, vaan älykäs kunnossapito vaatii ensin prosessien huolellista optimointia ja stabilointia.
– Koneoppimista pystytään hyödyntämään vasta, kun säätimet on viritetty ja varustettu oikealla tiedonkeruulaitteistolla. Automaatiojärjestelmän säätäjän toiminnasta kertova Overall Controller Efficiency -luku eli OCE kuvaa prosessin stabiiliutta, ja se sijoittuu aina välille 0–100 %. Tuotannossa on määriteltävä raja, miten alas luku voi laskea ennen kuin siihen puututaan, selventää Riikonen.
Kun ulos saatava data on validia, koneoppimisen ja simulaatiomallien avulla pystytään ennakoimaan oikea aika kunnossapidolle. Kun laite ei enää toimi, kuten sen pitäisi, datan laatu muuttuu. Kuluminen ja rikkoutuminen voidaan ennustaa ja laite korjata suunnitellusti, järkevänä ajankohtana.
– Jo pienelläkin datamäärällä huomataan, milloin prosessissa tapahtuu jotakin outoa. Kun dataa on kertynyt tarpeeksi, koneoppiva malli osaa ehdottaa, mistä häiriö voi johtua.
Turvallinen digitalisaatio mahdollistaa jatkuvan parantamisen
Koneoppiva analytiikka yleistyy vauhdilla. Mika Riikonen arvelee, että pudotuspeli alkaa jo lähivuosina: Jos teollisuusyritykset eivät ryhdy hyödyntämään koneoppimista ja tekoälyä ajoissa, kilpailijat voivat mennä todella kovaa ohi.
– Koko ajan on pystyttävä parempaan suoritukseen. Tekoälyn osaaminen ei yksin riitä, vaan tekijöiden on aidosti ymmärrettävä myös automaatio, mihin pystyvät vain harvat. Siitäkin syntyy oma haasteensa, että asiantuntijoita on toistaiseksi aika vähän. Mistä hyviä tekijöitä löytyy tarpeeksi, kun imua syntyy? hän huomauttaa.
Riikosen mukaan data-analytiikka on kustannustehokkainta, nopeinta ja järkevintä julkipilvessä, mutta ilman turvallista digitalisaatiota siihen liittyy riskejä. Insta on edelläkävijä nopeasti kehittyvillä turvallisen digitalisaation maailmanmarkkinoilla. Yrityksellä myös on pitkä kokemus niin prosessiteollisuudesta, instrumentoinnista kuin automatisaatiostakin.
– Turvallinen digitalisaatio mahdollistaa prosessidatan hyödyntämisen, koko säästöpotentiaalin ulosmittaamisen ja aidosti älykkään kunnossapidon. Puhumme samaa kieltä kuin asiakas ja pystymme hoitamaan koko ketjun kenttätasolta koneoppivaan malliin, Riikonen kiteyttää.
Oletko kiinnostunut teollisuuden datakeskeisistä ratkaisuista ja koneoppimisesta? Lue lisää:
Data-analytiikka ja tekoäly